Boeing 777 Flight Test stall cross wind full brake. Boeing has disclosed that their orderbook for the 777X program has lost 118 firm orders, leaving the company with 191 left on the books. The announcement comes less than a week after the company reported a $6.5 billion charge on the program; their first delivery has now been pushed back to 2023. The new Boeing 777X will be the world's largest and most efficient twin-engine jet, unmatched in every aspect of performance. With new breakthroughs in aerodynamics and engines, the 777X will deliver 10 percent lower fuel use and emissions and 10 percent lower operating costs than the competition.
Boeing 777 200 Youtube
The Boeing 777 is a large twin engine jet transport designed for regional and extended range service. The primary electrical system is a 3-phase, 4-wire, constant frequency 400 Hz, 115/200 Volt system, which has been the industry standard on commercial jet transports since the Boeing 707 (and maybe before, but that's as far back as I go). The neutral is connected to the airframe so that single phase circuits are supplied with a single wire, using the airframe as the return circuit. There is also a 28 Volt direct current system with the negative pole connected to airframe, such that 28 VDC services are also supplied with a single wire using the airframe as the return circuit. The 28 VDC power is derived from the AC power system by transformer-rectifiers.
The primary in-flight electrical source on the 777 is a 120 kVA constant speed two-pole brushless alternator. This represents a 33% increase in capacity over the next largest electrical source on previous Boeing commercial jet transports, the 747-400, 757 and 767. The alternator in these machines is integrated with an axial gear differential/hydraulic constant speed drive. The speed on the 120 kVA machine maintains an average 24,000 rpm plus or minus about 1%. This is currently the lightest weight technology in kVA per pound for supplying a 400 Hz constant frequency system, actually weighing just slightly less than the 40 kVA drive/alternator on the earlier Model 727. Minimizing weight has been achieved partly by increasing the alternator speed, partly by improved packaging and partly by switching from air cooling to oil cooling. The progression on Boeing airplanes has been from air-cooled 6000 rpm machines on the 707, 727, 737-100/200/300/400's and 8000 rpm machines on the 747-100/200, to oil-cooled 12,000 rpm machines on the 767, 757 and 740-400, and ultimately to 24,000 rpm machines on the 777. The 24,000 rpm constant speed Integrated Drive Generator, or IDG as it is referred to, was a mature technology also in service on the McDonnell Douglas MD-11 and Airbus A330.
The system on the Boeing 777 is configured with one IDG per engine, driven directly from the engine gearbox. There are two main electrical distribution buses, a left main bus and a right main bus, each normally supplied independently by their respective IDG. There is a third main alternator driven from an auxiliary gas turbine engine (called the auxiliary power unit or APU for short) located in the tail of the airplane, which is also rated at 120 kVA. Since the APU runs at a constant speed, this 24,000 rpm alternator is a direct drive, i.e., not an IDG. It is, however, essentially the same alternator used in the IDG. While the APU alternator is primarily a ground power source for the airplane, it can also be operated in flight to replace the loss of one engine driven IDG.
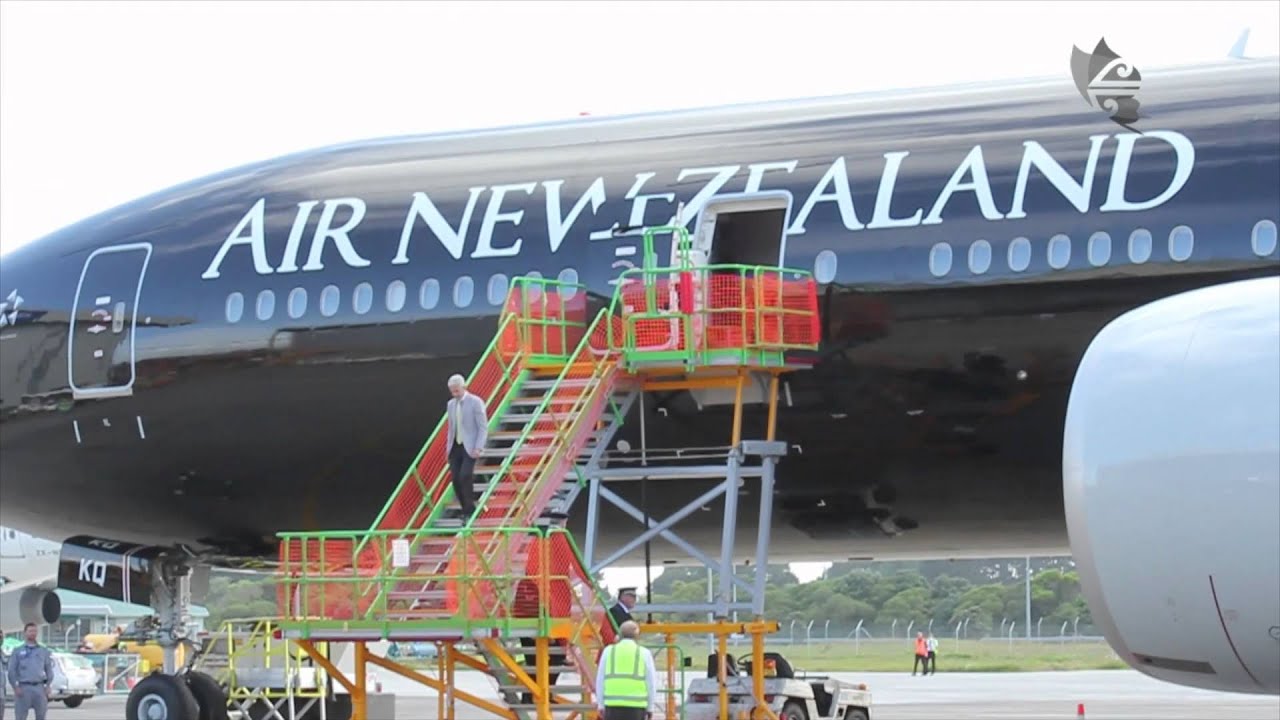
The 777 also incorporates a second power generation system, called the Backup System. This is a 25 kVA system intended to support essential services in the unlikely event of loss of all main alternators. A variable speed direct drive alternator was selected for this system to minimize the size of the engine installation. There is one backup alternator per engine directly driven from the engine gearbox at approximately 14,000 to 28,000 rpm. The output power of this alternator, at a frequency of 933 Hz to 1867 Hz, is converted to a constant 400 Hz by an electronic converter in the fuselage. Also incorporated within this machine are two permanent magnet alternators which are used as isolated independent supplies for the electronic flight controls system. Costabingo.
Flight instruments on the 777 are primarily powered by 28 Volts DC. Direct current power is supplied by three-phase transformer-rectifier units. There are four such units each rated at 120 Amperes. The choice of using 28 VDC instruments facilitates powering these instruments from battery power when necessary. Flight instruments and flight controls can also be powered from a Ram Air Turbine driven alternator which deploys automatically for loss of all engine driven generator power.
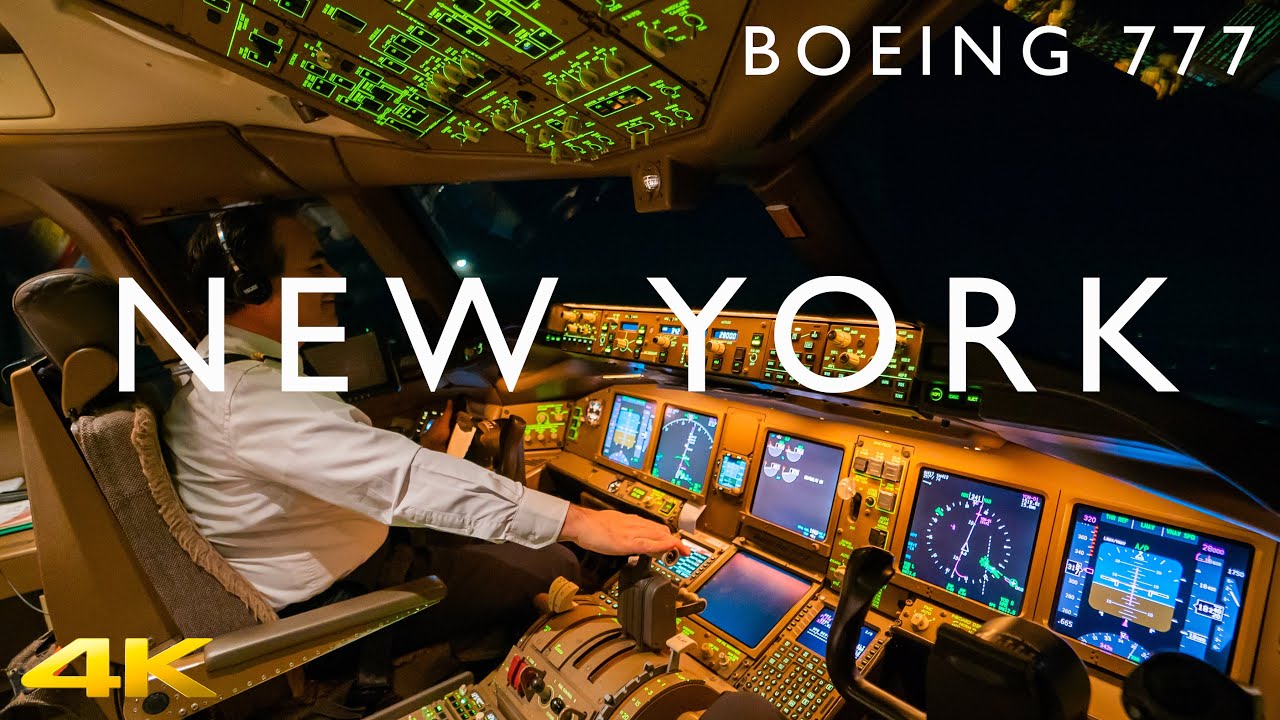

The Boeing 777 is a large twin engine jet transport designed for regional and extended range service. The primary electrical system is a 3-phase, 4-wire, constant frequency 400 Hz, 115/200 Volt system, which has been the industry standard on commercial jet transports since the Boeing 707 (and maybe before, but that's as far back as I go). The neutral is connected to the airframe so that single phase circuits are supplied with a single wire, using the airframe as the return circuit. There is also a 28 Volt direct current system with the negative pole connected to airframe, such that 28 VDC services are also supplied with a single wire using the airframe as the return circuit. The 28 VDC power is derived from the AC power system by transformer-rectifiers.

The 777 also incorporates a second power generation system, called the Backup System. This is a 25 kVA system intended to support essential services in the unlikely event of loss of all main alternators. A variable speed direct drive alternator was selected for this system to minimize the size of the engine installation. There is one backup alternator per engine directly driven from the engine gearbox at approximately 14,000 to 28,000 rpm. The output power of this alternator, at a frequency of 933 Hz to 1867 Hz, is converted to a constant 400 Hz by an electronic converter in the fuselage. Also incorporated within this machine are two permanent magnet alternators which are used as isolated independent supplies for the electronic flight controls system. Costabingo.
Flight instruments on the 777 are primarily powered by 28 Volts DC. Direct current power is supplied by three-phase transformer-rectifier units. There are four such units each rated at 120 Amperes. The choice of using 28 VDC instruments facilitates powering these instruments from battery power when necessary. Flight instruments and flight controls can also be powered from a Ram Air Turbine driven alternator which deploys automatically for loss of all engine driven generator power.
The Boeing 777 is a large twin engine jet transport designed for regional and extended range service. The primary electrical system is a 3-phase, 4-wire, constant frequency 400 Hz, 115/200 Volt system, which has been the industry standard on commercial jet transports since the Boeing 707 (and maybe before, but that's as far back as I go). The neutral is connected to the airframe so that single phase circuits are supplied with a single wire, using the airframe as the return circuit. There is also a 28 Volt direct current system with the negative pole connected to airframe, such that 28 VDC services are also supplied with a single wire using the airframe as the return circuit. The 28 VDC power is derived from the AC power system by transformer-rectifiers.
The primary in-flight electrical source on the 777 is a 120 kVA constant speed two-pole brushless alternator. This represents a 33% increase in capacity over the next largest electrical source on previous Boeing commercial jet transports, the 747-400, 757 and 767. The alternator in these machines is integrated with an axial gear differential/hydraulic constant speed drive. The speed on the 120 kVA machine maintains an average 24,000 rpm plus or minus about 1%. This is currently the lightest weight technology in kVA per pound for supplying a 400 Hz constant frequency system, actually weighing just slightly less than the 40 kVA drive/alternator on the earlier Model 727. Minimizing weight has been achieved partly by increasing the alternator speed, partly by improved packaging and partly by switching from air cooling to oil cooling. The progression on Boeing airplanes has been from air-cooled 6000 rpm machines on the 707, 727, 737-100/200/300/400's and 8000 rpm machines on the 747-100/200, to oil-cooled 12,000 rpm machines on the 767, 757 and 740-400, and ultimately to 24,000 rpm machines on the 777. The 24,000 rpm constant speed Integrated Drive Generator, or IDG as it is referred to, was a mature technology also in service on the McDonnell Douglas MD-11 and Airbus A330.
The system on the Boeing 777 is configured with one IDG per engine, driven directly from the engine gearbox. There are two main electrical distribution buses, a left main bus and a right main bus, each normally supplied independently by their respective IDG. There is a third main alternator driven from an auxiliary gas turbine engine (called the auxiliary power unit or APU for short) located in the tail of the airplane, which is also rated at 120 kVA. Since the APU runs at a constant speed, this 24,000 rpm alternator is a direct drive, i.e., not an IDG. It is, however, essentially the same alternator used in the IDG. While the APU alternator is primarily a ground power source for the airplane, it can also be operated in flight to replace the loss of one engine driven IDG.
The 777 also incorporates a second power generation system, called the Backup System. This is a 25 kVA system intended to support essential services in the unlikely event of loss of all main alternators. A variable speed direct drive alternator was selected for this system to minimize the size of the engine installation. There is one backup alternator per engine directly driven from the engine gearbox at approximately 14,000 to 28,000 rpm. The output power of this alternator, at a frequency of 933 Hz to 1867 Hz, is converted to a constant 400 Hz by an electronic converter in the fuselage. Also incorporated within this machine are two permanent magnet alternators which are used as isolated independent supplies for the electronic flight controls system.
Boeing 777 Landing Youtube
Flight instruments on the 777 are primarily powered by 28 Volts DC. Direct current power is supplied by three-phase transformer-rectifier units. There are four such units each rated at 120 Amperes. The choice of using 28 VDC instruments facilitates powering these instruments from battery power when necessary. Flight instruments and flight controls can also be powered from a Ram Air Turbine driven alternator which deploys automatically for loss of all engine driven generator power.